1. Terminology
"TEA" is abbreviation for Transversely Excited Atmospheric (pressure). It means
laser with transverse discharge and its chamber is filled with atmospheric pressure
gases. However there are many subatmospheric or even lower pressure lasers referenced
as TEA-type. Whats up? Where is the real border between TEA and TE lasers?
As it was Shown by Beaulieu himself (e.g. see US patent N4143337) the top power
of gas laser rises as a square of pressure. It happens due to increasement of active
moleculas number and also due to reduction of light amplification time. Hence at high
pressures it becomes possible to build rather compact megawatt class pulsed lasers.
The action of megawatt laser radiation is also completely distinct. When the power
of low pressure lasers smoothly heats (and melts) materials, the megawatt pulses from
high pressure lasers immediately vaporize and ionize thin surface layer. It looks like
glowing of objects in the field of laser beam, Being focused the laser pulse can
optically break transparent media. When the power it enough it is possible to ignite
a "laser spark" in open air. Mainly for such brilliant effects the TEA-lasers are used.
So the lasers are defined mostly by their effects. And the border is rather comparative.
When laser beam causes things to glow or sparks in the air when focused, the laser will
definitely be referred as TEA type. On the other hand if power is rather small and effects
are similar to ones fom continious wave laser, the one will be only TE type (provided
that it uses transverse discharge).
Also one may say that TEA lasers operate in gain modulation mode when TE lasers
operate in continious pum drain mode. But explanation of these terms would be too
complex to be placed here.
2. Brief description of the laser
Here You are offered to construct a miniature molecular gas laser of subathmospheric
pressure excited by transverse discharge (TEA-laser). The laser uses carbon dioxide as
an active medium. Need to say that if we are restricted by those kinds of lasers that
can be constructed without usage of commercial hi-tech products (such as laser crystals,
laser diodes or interference laser mirrors) the CO2 molecular laser ith the one and
single that can provide enough power to show noticeable effect on something other than
sensors or photosensitive materials. It differs distinctly from the nitrogen laser which
is well known to the amateurs. CO2 laser can drill holes and cut thin materials. And
moreover the described here TEA laser can show effects of powerfull laser radiation
that one can not reproduce using, say, high power laser diode. First of all it is laser
ablation (surface vaporization) and laser spark (for large variants). Such phenomena may
be reproduced by Q-switched solid state lasers but they are expensive. Or either by
the same (but bought) TEA-laser, but small sized TEA lasers of are strangely absent at
the market.
The laser described here is not the best neither the most powerfull nor the smallest.
But it seems to be the most simple to produce and assemble. The laser shows the next
parameters (related to opereation on helium containing gas mix are placed in brackets):
Operating wavelength: 10.6 micrometers
Output energy: 10 mJ (50mJ)
Output power: ~100 kW (300kW)
Repetition rate: ~10 Hz
Operating pressure: 300 Torr (760 Torr)
Gas mix: CO2:air 1:1 (CO2:air:Helium 1:1:5)
The transverse cross section of the plasma tube is given on Fig 1. It shows the
technique how to obtain the volumetic discharge.
"Fig 1"
The main discharge volume is formed between the profiled anode and profiled cathode.
Preionization is made by ultraviolet radiation of the sliding corona discharge. The last
is forming around the anode in the area of strong electric field. The area of strong
electric field is artificially created by placing a special strip preionization electrode.
It is placed near the anode at the opposite side from the cathode. And the preionization
electrode is separated from the anode only by thin film of stron dielectric (mylar).
Mechanical strength of the assembly is provided by two plexiglass plates. The whole device
is sealed into plastic pipe to be vacuum tight. The section of the plasma tube along
its axis is shown on fig 2.
"Fig 2"
The plexiglass plates are plased near the axis of the tube. In order to provide low
inductance and low resistance the tube has multiple terminals and they are made from
large screws. The rear mirror with its vacuum tight alignment mount is placed directly
at one end of the plasma tube. Other end carries an output window.
Schematics of the power unit is shown on Figure 3.
"Figure 3"
C1, C2, ... Cn - low inductance low loss capacitors. They are used as energy
accumulators. Cp - peak capacitors. They also must have low inductance but the
requirements for low losses is less strict. The total capacity of energy accumulators
is 1000.. 1200 pF per centimeter of active length of laser electrodes (15200 pf for
the presented laser size). The total capacity of peak capacitors is set to 1/10..1/20 of
the main capacitors capacity (1180 pf for the presented laser size). SG1 is air spark gap,
it uses air as a working gas, operates at atmospheric pressure and enclosed to reduce sound.
Its discharge length should be adjustable in range from 2 to 5 mm. The whole unit is powered
by 12..15 kV DC voltage.
The gas scheme is shown on Figure 4.
"Figure 4"
The gas mix vessel is filled by a premixed gas mixture or either the gas mixing
process takes place directly in it. The V1 and V2 valves are used to control gas line.
The vacuum pump provides necessary pressure and also used for preliminary cleaning
the laser volume from air. Once being filled with working gas mixture the plasma tube can
operate in a sealed off mode for a certain time When V1 and V2 are closed.
3. Materials
To built the laser You will need the next resources:
- A piece of aluminium strip 10 mm wide 2 mm thick and 250 mm long
- A piece of aluminium strip 15 mm wide 2 mm thick and 270 mm long
- Two plexiglass or fiberglass plates 42 mm wide 5 mm thick and 300 mm long
- A little piece of plane plastic. It must be evenly thick (plano parallel)
(a rectangular piece 20x40mm sized would be enough)
- Plasic sewers tubing, 50 mm in diameter and not shorter than 300 mm
- A piece of rather plane plastic (this one is not necessary to be plano-parallel).
It should be 7..15 mm thick and more than 80x170 mm sized
- Aluminium duct tape 50 mm wide (the narrow one) and 100 mm wide (the wide one)
- Double sided duct tape.
- Epoxy glue
- Glue gun rod (the white one)
- Mylar sheet. It should be thicker tham 100 mcm and not less than A4 format. (It is rather
spread as laminating material).
You may need the next tools: scissors, jigsaw, a drill with a set of bits, a glue gun,
vernier caliper, a ruler (not shorter than 300 mm), a marker, a sandpaper (rough one
and fine one), felt disc and polish wax.
It is not bad to get a radio soldering tool and an aluminium soldering flux.
The aluminium strips are used to produce the laser electodes. They are one of the most
important laser parts. The main requirement to the strips is to be straight, straight, and
straight again. If You are ready to work hard then use steel strips to make electrodes.
Plexigalss or fiberglass plates are used to make electrode keepers. Straightness and
hardness are important here too. The length of plates should be at least equal to the length
of electrodes. Width of plates is defined by suitable placement inside laser tube. If needed
the plates may be made narrower but You will meet problems with their fixation. Thickness
of the plates is defined by their necessary strength and to some extent by needed value of
parasitic capacitance of the scheme. In any case the plates should not be thinner than 3 mm.
If You can not get suitable plastic sheets at least use window glass.
The plane parallel sheet of plastic is needed to make intermediate props setting the
distance between electrodes. The parallelism of electrodes depends on equality of props
heights. In principle one can make props independently and then fine tune their heights by
presize cutting but it is boring.
The sewers tubing is used as a vacuum tight body of the laser. It is the best and simplest
solution among ones tested.
Another plastic sheet is needed to make vacuum tight rear mirror mount. Here the reguirements
for sheet to be plane and parallel are weaker. On the other hand the material should be hard
enough to endure forces arizing in alignment process. Not bad if You can see the discharge through
the alignment unit, so transparency is a good option. Practically plexiglass is the best material
for rear mirror mount.
Naroow aluminium duct tape is used for wiring of laser. It is wide spread and easy to get, so
there's no need to replace it with anything. The wider aluminium duct tape is used to make
preionizing electrode. When it is unaccessible the preionizer may be made from rather thick
aluminium foil but it will be more difficult to set it in place.
Epoxy glue is used to fix nuts in mirror mount. Choose the most strong from available ones.
Sealing of junctions is better to be made with glue gun (choose the white rods they are harder
and stronger.)
4. Construction
Making the electrodes
Cathode is to be made of a shortcut of aluminium strip 10 mm wide 2 mm thick and 250 mm long.
The sequence of actions to produce the cathode is shown on Fig.5.
"Figure 5"
At first the strip has a rectangle section. (Fig. 5a) Using not a very rough filer make two
bevels along both sides of the aluminium strip. Bevel angle is to be 45 degrees. And the bevels
should be straight and even all way long. Natually You can not do this perfectly without a milling
machine. However try to make the bevels straight and even. Then using the same filler round the
just formed edges. Also try do round evenly all way long the electrode. If grinded and polished
this electrode may already be used in laser. However the gas discharge will be not uniform -
more dense near sides and more sparse near center. Moreover the top limiting pressure (the
highest pressure at which one can obtain volumetic discharge here) will be slightly less than it
could be.
Further upgrade of the electrode is made by means of reduction its thickness by 0.3 mm at sides.
Smoothly make two wide and shallow chamfers from near the center line of the cathode (2mm from
it to be more precize) and to the side edges. (As it said at sides You shoud take 0.3 mm deep)
(Fig 5d). Then the obtained figure is to be rounded again to get smooth profile. Longtitudal
edges need to be rounded too. After this upgrade the electrode is about to follow the Chang
profile with curvature factor of 0.07. (Fig 5e). At last You need to grind the electrode with
sandpaper and then polish it with felt disc untill it shines as a mirror. (Fig 5f.)
The ready to use electrode looks like it is shown on figure 6.

"Figure 6. Cathode."
Anode is to be made of a shortcut of aluminium strip 15 mm wide 2 mm thick and 270 mm long.
Yes it is slightly wider and longer than cathode. And a bit simplier. Make actions same to
shown on fig 5a - fig 5c. Then grind and polish to mirror like shining. Longtitudal ends
are also to be rounded and polished. However when rounding longtitudal ends You need not be
so precize - there is enough space to round it freely. Just round them as You like.
The ready to use electrode looks like it is shown on figure 7.

"Figure 7. Anode."
You should get that neither electrodes profiling nor their polishing and even preionization
can not be considered as a true method of prevention of volume discharge contraction. Using
the lexic of role playing games: "The Chang profile is plus ten to spark defence". Good
polishing is another plus ten. And the preionization is even more plus (its value depends on
preionization level and correctness of its timing). So step by step You getting to laser
operation conditions. Scratches on the electrodes do not cause sparking provided that they
are good polished all depth to bottom.
Assemblage of cathode unit
The cathode unit is very simple. Get one of the plastic electrode keeper plates, attach the
cathode there (make sure that midline of the cathode and midline of the plastic plane coiicident)
and then make the necessary wiring to conduct electric current to cathode.
It is suitable to make it this way:
- Cut a strip of aluminium duct tape 10..15 mm wide and 80..100 mm longer than length of electrode
keepeng plate. Stick the duct tape along the plate midline. The surplus endings (40..50 mm at each
side) turn and stick to another side of the plastic plate. The continious aluminium strip forms
cathode terminal bus of the unit and the endings carry current to the electrode.
- Attach cathode to electrode-keeping plate by means of double sided dudct tape. The area of the
cathode that will lye above current carriers leave free from the duct tape. See Fig 8.

"Figure 8. Assemblage of the cathode unit"
The ready to use cathode unit is shown on figure 9.

"Figure 9. Cathode unit ready."
Assemblage of anode unit
Anode unit is more complicated due to the preionizer electrode mounted on it. The preionizer
is cut from wide aluminium duct tape. The preionizer should be wider than anode by 6 mm (each
side steps out from besides anode by 3 mm). Also the wiring from the preionizer to cathode pole
of the scheme must have low inductance. To prowide such a wiring You will make two (or more by
Your choice) side branches. The width of branch strips (wings) should be not less than 10 mm and
they should be lon enough to reach cathode bus. If making multiple wings place them equidistantly
along length. If wings were soldered to the preionizer the unnecessary hills would appear. So You
need wide aluminium tape to cut the whole preionizer with it wings (Fig 10).

"Figure 10. Anode and preionizer"
Stick the preionizer onto the electrode carrier plastic plate as it shown on fig. 11.

"Figure 11. Preionizer inplace"
Using a double sided duct tape and a sheet of mylar cover the preionizer with insulation layer.
The scheme has a tendency for sliding breakdown from anode to current carriers of the preionizer
especially at low pressures. So when cutting out the mylar dont forget about insulation wings.
Te insulation wings should cover additional 15 mm at each side of conductives. See fig 12.

"Figure 12.Insulation of the preionizer."
The assembled preionizer is shown on figure 13. The view is from electrode keeper side.

"Figure 13. Preionizer ready."
Above preionizer covered with dielectric do attach anode current carrier and the anode itself.
Act like when You did during cathode unit assemblage.
The ready to use anode unit is shown on fig 14.

"Figure 14. Anode unit ready."
Gas discharge unit assemblage
The anode unit together with cathode unit placed at proper distance and with proper electrical
connections we will call as "Gas discharge unit". To make it You will need a number of little
distancing props. Cut them from plane-parallel sheet of plastic 10 mm thick. The number of the
props should correspond to a number of preionizer wings - You need two props for each conductive
belt. But not less than six. The height of the props is 10 mm and other dimentions are rather
free provided that they stand stable and they do not interfere with other items placement.
The props are shown on figure 15.

"Figure 15. Distancing props."
Cover the plane edges of the props with double-sided duct tape and attach them onto the anode
unit. The props should stand at the middle and at the places where conductive wings lye.
(If there ara more then two conductive belts then the additional intermediate props may be
omitted) See fig 15.2.
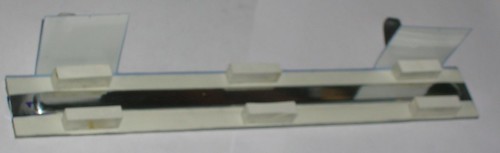
"Figure 15.2. Props placement"
Next put the cathode unit over the props. Align so that anode and cathode were parallel and
the cathode was above anode's centerline. Bend preionizer wings to attach them to the cathode
current carrying bus. Fix all the module with duct tape. Place turns of the duct tape over
the props placement, otherwise not compensated forces will bend anode or cathode units.
The complete gas discharge unit is shown on figures 16, 17. Even if it can be viewed on the
pictures it is not necessary to solder there. Mechanical contact is enough.

"Figure 16. Gas discharge unit assembled."

"Figure 17. Gas discharge unit. End view."
The attachment with usage of double sided duct tape has shown itself to be pretty strong. The
complete discharge unit endures e.g. drop to the floor from above 0.5 meter. If the electrodes
attachement appears to be weak in the best case it means that the duct tape is bad and need to
be exchanged by other similar produt. In the worst case (and usually) it means a curvature of
the electrodes or (and) their keeper plates. If they not become straight when relaxed (when
fixing duct tape is cut off) then they are unusable and need to be replaced. It is very hard
to get volumetic discharge with randomly curved electrodes.
Place the complete gas discharge unit into plastis sewers tubing (50 mm outer diameter) and fix
there by contact screws. There s no need to use nuts. Just drill holes wis a bit smaller diameter
than the outer duameter of screws' thread. The screws will thread plastic of the dube themselves.
The turning force applied to the screws should be enough to fix the discharge unit but not so
strong to bend it. (When assempling keep an eye on this.)
Close one end of the tube with mirror alignment mount and close the other end with a plastic
sheet with suitable hole for a window. The design of the rear mirror alignment mount is rather
trivial and will not be described here. Refer to photos for details if needed. The window on the
other side of tube should have ~10mm diameter. It needs to be transparent for both visible
and mid infrared light. The infrared transparency is for laser generation output and the visible
one is for alignment. You can use a ZnSe window as on photos or use thin polyethelene film as
well. 20 mcm Teflon film gives good results too. (Mylar or vinyl or either acrylic films arent
transparent for this laser radiation. Dont use them.)
When choosing the film for window pay attention that the lower it scatters visible light the
better for mirrors alignment process. The film must be strong enough to endure athmospheric
pressure (usually at least 20 mcm thick). Clear at a glance plyethelene or teflon films having
necessary thickness are pretty rare so You may need hunt them for a while. Of course in the
worst case You may fall down to use the second vacuum tight mirror mount on the other end of
plasma tube similar to the rear mirror mount. It definitly will lase but will be much less
handy.
If found a suitable window dont attach it yet. Make a temporary lid from a suitable piece
of plastic or even a coin. Seal all outer joints with glue gun. If done carefully and
correctly the laser will become vacuum tight from the first time. Otherwise use Your bath
and tire pump to find leakages. (Thats why it is not recommended to install rare windows and
mirrors at early stages. The bath and washing are definetily of no good for them.)

"Figure 18. Laser tube in the process of sealing"
When done with the leakage sealing and the tube is vacuum tight with the temporary lid (lids)
then replace temporary lid with the infrared window. Check for leakages again. If it leaks
remove the window and glue it back. Repeat the process untill it becomes vacuum tight.
On this stage obviously You can not bath Your laser. Instead use vacuum pump and some
vacuum measurer. Because all other leakages are stopped if the vacuum system leaks it means
that the last thing (the newly glued window) is not tight enough. This way You can perform
dry tests for tightness.
If a temporarey lid is installed in place of the rear mirror repeat the procedure with this
one too. Do not try to vacuum seal both ends at a time - You will never know which one leaks.
After sealing the laser tube is complete and ready to use. Its time to build other parts of
laser. On figure 19 the complete laser tube is shown. Fig 20..23 show details of the laser
tube design.

"Fig.19. Laser tube complete"

"Fig 20. Rear mirror mount"
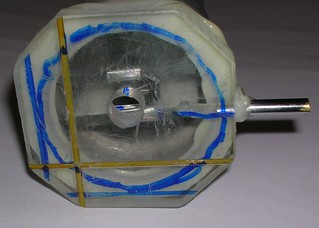
"Fig 21. Output window place."

"Fig 22. Rear mirror mounted."

"Fig 23. Output window mounted."
Hints about making the rest parts of the laser
In order to make the complete laser in addition to the laser tube, You also need good hard and
strong basement to place it onto. If the laser tube contains one mirror and one window You will
need a front mirror and its alignment mount too. The high voltage pulser power supply must be
assembled having as low inductance as possible so it becomes namely a part of the laser.
Pieces of profiled metal are good for use as the basement. You can take rail, angle, box etc.
To be hard and strong the aluminium part should be 4..5 mm thick. Steel one may be thinner.
It is suitable to use standart attachment clips for toilet tubes to fasten the laser tube to the
basement. The elastic elememt may be formed by three pieces of little spring or even by rubber
gasket around the central hole (as it was done in rear mirror mount). Details are in this guide.
The accumulative capacitors are placed directly on the metal basement of the laser. The
capacitors are to be of low inductance (low ESL) and low resistance (low ESR) type. The special
pulsing doorknob capacitors (e.g. Murata N4700 type) are good. The other types of doorknob
ceramic capacitors (e.g. the ones from old tv sets) are usually worse but usable. The
rolled foil capacitors are usually unusable. If You can not get a suitable capacitor You
can make it yourself: handmade planar foil capacitors or the rolled ones with 'candy' type
terminals can have acceptable low inductance and enough capacity. However with them You will
need to puzzle over the low inductance design of the laser feed circuit.
The peaking capacitors are placed strictly near the spark gap, forming the complete unit with
it. To ensure low ESL and low ESR all wiring in laser is made by wide strips of aluminium
foil or aluminium duct tape. (Thanks Goodness at pesent times we can easily solder aluminium
parts with this magic aluminium flux)
The fully assembled laser is shown on fig 25.
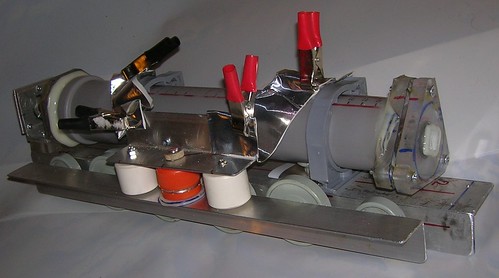
"Figure 25. Laser complete."
5. Gas mix
Dependently to gas purity and mix contents first of all the maximum pressure changes at
which laser can work. Also output power and energy are different too. The mix of pure
CO2:N2:He at 1:1:3 (volumetic parts) is about to be optimal for this type of laser.
However the laser havent been tested yet with tis mixture. Mostly due to difficulties
to obtain pure nitrogen at home.
The nitrogen in the mixture may be replaced with common air with correspondent reduction
of laser parameters. The electronegative oxygen gas drastically decreases the effectiveness
of preionization. It causes discharge instabilities and shrinking of the discharge column
even in cases when the volumetic discharge is rather stable. Moreover the range of pressures
where the volumetic discharge is obtainable moves towards lower pressures. To some extent
it may be compensated by increasement of helium part in the mixture.
The laser is operational at athmospheric pressure using the CO2:air:helium 1:1:5 mixture.
Without helium the laser is operational at pressures below 300 Torr.
Need to say that practically it appears that "vacuum is better than helium". 300 Torr is
a bit less than a half of athmospheric pressure and is easy to obtain by any kind of pump
capable to pump out gases.
Water vapours in very little quantities are good for laser generation, but with increasement
of their concentration there are losses of laser power and even stop of lasing. For example
when one of gases in CO2:air mixture is saturated wet (at room temperature), we have a
mixture that does not lase in this laser. (Probably it will do in some other kind of laser
who knows.) This means that we can not use the beloved by chemists method of gas easuring
and mixing in a bottom-up vessel placed with its neck into water. It is due to the fact
that the gas bubbling trough water becomes wet to saturated level. It also means that the
most popular way to obtain carbon dioxide by mixing baking soda with lemonic acid is
unacceptable too. At least if You intend to use some wet method of gas obtaining or mixing
be sure to use a gas drying patron at laser tube entrance.
Much easier to get operational gas mixture using a dry way. One can use CO2 cartridges from
pneumatic guns as a source of carbon dioxide. The 8 gramm cartridge contains up to 4 liters
of the gas and the 12-gram type cartridge - up to 6 liters. Usually due to the low grade
of cartridges and due to unavoidable losses You obtain about a half of named numbers.
The cartridge is to be poured to the gas mix vessel by one way or another. One can use
pneumatic gun and in the most mean case just shoot its contents into the vessel. Better
to use a household saturator (a device for making soda water at home, see fig 26).

"Figure 26. The water saturator"
The volume of the vessel should be choosen with taking into account the volume of CO2 from
the cartridge and the necessary dilution by other gases. To avoid the necessity to evacuate
large gas volumes it is better to use gas vessel made of flexible material (party balloons,
car tires and so on). Good blown rubber balloons have abot 10 liters of volume (there exist
pretty large species up to 16 liters). Light weighted car tires have 5..7 liters volume
(at athmospheric pressure inside).
The athmospheric air suits well for the gas mixture. When good weather (no rain, no fog) its
humidity is acceptable. No need to wait for sunny day. Use car pump to move the air into
the gas vessel. The necessary volume can be estimated by the balloon perimeter (this approach
is used by Jarrod Kinsey) or either by number of pump hits (the way i usually do it myself).
In the second case use the next algorythm:
- pour the CO2 cartridge into the tire.
- visually determine the obtained volume of CO2;
imn order to do this take another tire of the same type and pump it using hand driven
pump until it visually takes the same shape as the one filled with CO2. Count the pump hits.
When You see that both ires are filled equally stop pumping and write down number of
pump hits. You will get the voulume of CO2 measured in units of the pump hits.
- Next calculate the necessary air volume in the units of the pump hits (usually it is a
half of CO2 volume or, sometimes, equal);
- connect the pump to the tire with CO2 and pump there the necessary amount of air.
The triple component mixtures require more complex procedure, but the same idea works good
there too.
6. Alignment
Alignment of the laser mirrors is rather trivial and marginally differs from the same process
for other types of lasers. The laser has comparatively large lightpass cross section and is
very forgiving to the alignment biasing when using stable cavity type.
Four moments to pay attention to:
- The electodes are parallel to each other, they are wide and almost plane. Moreover they
are well polished. It provides massive parasite reflection between them. When laser is
aligned onto a parasite reflected beam spot, it would not work. (Longer lasers made by the
same scheme have higher gain and really can lase with beam bouncing but power losses are
huge). Sometimes it is really hard to distinguish the main spot of the alignment laser
from the bounced one. When done with needling the alignment beam through the laser being
aligned, do three times check whether You see th correct spot or not. And only then
continue the alignment process.
- When using polyethelene or especially teflone output window the spot of the alignment
laser is rather dirty and the precision of the alignment drops down. If the stable cavity
is used (concave-concave or concave-plano mirrors configuration) then the achievable
alignment precision is quite enough for lasing. It worse if plao-plano cavity is used.
In case of completely low transparency of the output film it can happen that it is difficult
even to see the spot of beam reflected by rear mirror. In this case it is impossible to align
the cavity by common way. That kind of films is better not to use.
- Always perform alignment process only after the laser have been tightly installed onto
the selected place and already connected to all pipes and wires. If You have to do this
after the alignment, You have a high chance to break the adjustment.
- The rear mirror alignment is good to do under vacuum (at the working pressure which
in most cases is below athmospheric). This is due to misalignment appearing due to
atmospheric pressure loadings on the rear mirror plate. When aligned properly (with proper
tight forces on the adjustment screws) the rear mirror keeps position rather good in
large pressure range. However in any case its tilt is not equal to zero. So better to
set it up at working pressure.
Another note for those who like fixed rear mirror mounting. - Dont. Think about the fact that
You spend Your efforts to make an adjustable mount only once (in life of the laser). And You
will spend Your efforts to make proper mirror alignment every time You use the laser. The
adjustable rear mount reduces alignment difficulties greatly. Once You made it You will
never regret it.
When alignment is complete do not remove the alignment laser. Its beam will be very usefull
to show where the invisible infrared beam of the CO2 laser goes.
7. First Light
Lets assume thad the laser is assembled, aligned, connected to the power source (of cource it
is turned off for now) and included to a gas contour as shown on fig 4.
The very instrument to observe the lasing is calorimeter power meter. If You have no commercial
one, the simpliest way to build it is to use a peltier processor cooler element and some cheap
multimeter. Refer to my other guide how to do it correctly. At the beginning the calorimeter
is a must. Later You will obtain a laser beam that produces effects that can be seen by naked
eye, but befor it happens You most probably will need to adjust the main spark gap settings,
the pressure and may be the mixture contents. So dont hope that when laser works You immediately
see that. Use calorimeter and adjust for maximum power. And suddenly You will see the beam
spot.
Install the calorimeter a front of output mirror. Use the red beam of alignment laser to
set the target at the correct position. Turn the vacuum pump on and open the exaust valve V1.
Evacuate laser up to maximum vacuum that can be reached by Your pump. Shut the V1 valve and
open the V2. Let the gas mixture enter the laser tube. Dependently to the limiting vacuum it
may take several cycles to wash the tube properly and to fill it with the gas mixture.
Shut the V2 and slightly open the V1. Watch manometer M1 while setting pressure of about
500..600 Torr. Then adjust the spark gap SG1 (fig 3) for the voltage to be just enough to
spark between electrodes in the laser tube. Switch the power on for a short time to check up.
(If it powered on longer You can severely damage electrodes)
ADJUSTMENT OF SPARK GAP IS TO BE DONE ONLY WHEN POWERED OFF AND ALL ACCUMULATIVE CAPACITORS
ARE DISCHARGED!!!!!!!!!!!!!!!!!!!!!!!!!!!
Then lower the pressure in the laser tube until getting volumetic discharge. Usually it
appears at pressures of 200..300 Torr when without helium. To watch the discharge (as it was
said earlier) You should have transparent rear mirror mount or either some other window in
the tube. The vacuum meter is quite usefil when starting the laser. Even a very rude one
made by means of readjustment of some welding acetylene manometer.
If all goes well then the calorimeter will indicate some power as soon as diffuse discharge
is obtained. If there's no lasing then try to reduce pressure to 80..100 Torr. With pressure
reduction the gain rises and it is easier to get gerneration.
If volumetic discharde presents and there is still no lasing, first of all check the gas
mixture. Not all mixtures are operational. Moreover there are certain troubles with their
storage. For example co2:air mixture dies after twoo weeks storage inside car tire.
If You are sure that the mixture is good, try to check the alignment. If the alignment is
also good then probably cavity losses are too high (the output film window is probably not
transparent enough or either the mirrors have not enough reflectance). Change irror(s)
or (and) the intracavity window, reassemble laser and try again.
When You have no manometer try this:
Set the SG1 to the 1.5...2 mm of the gap value. Pump the tube off and turn power on from time
to time. Eventually the spark discharge inside the tube wil turn to a diffuse one. When
doing this You should switch the power on only for a short time in order not to damage
electrodes with the spark. If the volumetic discharge is unobtainable at any pressures then
the gas discharge unit has a breakdown somewhere in insulation. (It may happen when rudely
assembled.) Dismount the laser, find the breakdown place (it can usually be easily seen
as a burned place) and change the failed parts. The electrodes may need to be repolished.
Note that new laser gives a nice smooth purple violet discharge in a certain pressure
range (60..350 Torr). But it does not mean that it will always behave this way. As a rule
after some work the glossyness of the electrodes becomes broken (mainly due to damage by
spark at improper pressures) and the laser begins to spark. Dont be upset about this.
When the spark is rather weak and is positioned aside from the beam's way and when there
is good purple glow can be seen, laser usually works good regardless of such kind of
spark. However when the spark is strong and the violet glow is hard to be seen (or is absent
at all) it means that the electodes need to be restored.
OK then, lets assume that You finally obtained lasing. Then You need only to adjust
parameters for the highest output. Just vary pressure and spark gap SG1 breakdown voltage
to get maximal energy or power. Note that points correspondent to maximal pulse energy
(maximal average power) and maximal pulse peak powe do not coincident. Tune the laser to
what You need.
At last when You are familiar with working on co2:air mixture You can go and buy some
helium to get better results.
8. Scaling
- The laser can easily be scaled towards increacement of the electrodes width. The
accumulative capacitors' capacity can be increaced in proportion to discharge column width.
Output energy is almost linear to the discharge width (and pump level). However it is true
only when semitransparent output coupler is used. If front mirror uses a hole to output
the radiation, the output power only slowly rises with discharge width. The highest boundary
of volumetic discharge pressure range marginally decreases with widening the electrodes.
It must be said that when the electrodes are processed by hands it is quite hard to
maintain their shape in such an order that the discharge column width is in linear
proportion to the width of the electrodes. Usually the predictability of the discharge
width is low especially with electronegative gas mixtures.
- With miniscule changes this laser is comparatively easy to scale in length. The
accumulative capacitors' capacity can be increaced in proportion to length of the electrodes.
(If electrodes are kept straight the longtitudal size of the discharge follows the length
of electrodes smoothly.) The output energy grows differendly dependent to conditions. With
low loss cavity it should be proportional to the length (and pump level). On the other
hand at typical for homemade lasers conditions (large enough losses) the output energy
grows stronly and non linearly.
When scaling in lenth one should pay attention for keeping the inductance of wiring as
low as possible. Otherwise the 40 cv long laser becomes unstable. The reduction of the
wiring inductunce in the design described may be provided by the next way:
The conductive belts are added that connect terminal buses (ones that in contact with
terminal screws) with the electrodes. The belts are to be made of aluminium foil strips
(not narrower than 15 mm) and are placed each 15 cm or more frequently. Other solutions
for lowering the wiring inductance are also possible.
When length of the laser approaches one meter the point type spark gap may appear to
have too high inductance. Try to use a rail type spark gap or a number of paraller
point type spark gaps sychronized by common ignition.
- When simultaneously scaling to width and length the electrical capacity between anode
and preionizer becomes considerable (or even higher then the one of peaking capacitors).
It may severely interfere with operation of powe supply scheme. It shows as too low
pressure when volumetic discharge is achievable (40..60 torr) and its ununiformity
(it looks cloud like turbulent and with stong brightness variations). In this case it
is needed to reduce the anode to preionizer capacity. The excessive conductive material
of preionizer should be then removed from under the anode. It is handy to do it when
the preionizer is already stuck to the keeping plate. Cut a closed contour line in it
using a sharp blade. Then remove foil from the just made window. This way one can
succeed in keeping operational comparatively large samples of the laser (400x20 mm).
- Scaling to enlarging the discharge gap without rising the pump voltage is easy
(by pressure reduction) but in most cases is senseless.
Scaling with correspondent voltage rise meets an obstacle dure to difficulties in
keeping short the time of SG1 spark gap switching with. Probably it can be avoided
using multigap rail type discharger. Also need to say that when increasing the
distance between laser electrodes their thichness should be increased as well. It is
necessary that the distance between electrode carrying plates was 30%..40% greater
than one between the electrodes. Otherwise sparks can appear directly between conductive
buses of cathode and anode units.
- Scaling to lower sizes. The minimal length of the laser is determined mostly by
its intracavity losses. With aluminium mirrors and teflon window the 200 mm electrode
length is about to correspond the threshold of lasing. With high quality dielectric
mirrors the length of the electrodes can be set to 100 mm or even less.
The minimal width and heigth of the discharge are limited by diffraction losses and
should be choosen from the next condition:
{ S>3..4*sqrt(L*lambda); H>3..4*sqrt(L*lambda) }, where L is distance between the laser
mirrors, lambda=10.6 mcm - is the co2 wavelength.
9. Applications
"Not so powerfull to cut it all off, but is quite a drill when focused!" - was said about
this laser. When repetition rate is high it drill holes in most thin materials in reasonable
time. The most amazing thing is that it can drill the holes invisible by eye (less than
100 mcm in diameter). Only narrow He-Ne beam can unhide the hole for You. On one hand it is
the evidence that the beam quality is good and on the other hand it is a unique way
to drill so narrow holes. Also laser is handy while drilling hard materials such as tungsten
or ceramics or gems. A friend of mine dreamed about making beads of jewels but could not
find a suitable way how to drill a ruby.
Naturally my fantasy ends when I think about home applications of the laser other than
some kinds of special drilling.
However unfocused beam produces glowing spot almost on all materials. See Fig 26. It can
remove coatings (but too slow for practical uses). It can be used for sputtering metals or
dielectrics for making some coatings (e.g. mirrors) but You are to have a suitable vacuum
chamber with a good IR-transparent window. However electron beam or cathode sputtering do
the same job as well but much simplier to construct.
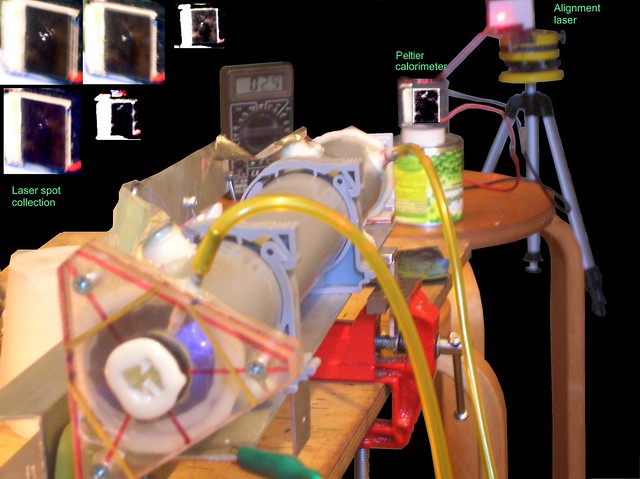
"Figure 26. Laser in operation"
Larger samples of the laser empowered by helium mixture can produce laser sparks in air
when focused by lens having 50..60 mm focal length. Quite a show but usefulness is doubtfull.
Still CO2 laser is the one and single type of laser that can be made completely from scratch
at home and that have enough power to drill burn and cut something.
On the other hand the spectrum of this laser professional applications is very wide. One
can use it as a light source for spectral calibrations and measurements, for chemical
reactions initiating, and even for laser radar.
The main obstacle in applications is indeed the fact that usual glass is opaque for CO2
laser radiation and the common detectors (photodiodes, protoresistors and phototransistors,
except cryogenic ones) are insensitive to it.
10. Appendix
Some points of laser design that should be paid attention to:
- Note that all edges of high voltage parts must be rounded. Including the basement of the
laser, its terminals and even aluminium foil strips. Sharp edges arise risk of breakdown,
and even if You do not see sparks, there are severe losses to corona at them. Lets consider
it as a native element of high voltage culture, that must be implemented always until other
is definitely needed.
- Vacuum is better than helium. Again vacuum is really better than helium. After several
tens of trips to a nearest shop for party balloons You will understand this fact. Well, if
You got a friend at local gas station or Your job specifics presumes that any time You can
put Your paws on a gas cylinder then You can almost ignore this. But even in this case...
Helium is pricey and cylinders are heavy...
Usually it happens like that: You someway get helium, try Your laser working on helium mix
one or two times. Then You are happy that laser can operate at athmospheric pressure and can
give rather high energy. After You are happy enough, You continue to use the laser at low
pressure but without helium.
- Pay attenction for strict vacuum tightness of laser tube and all its joints and connections.
The working vacuum isnt deep and You surely can keep it by continious pumping even with severe
leaks. But in this case You will have uncontrollable gas mixture contents. Sometimes one can
achieve lasing with not tightly sealed tube, but it lasts for seconds and it takes a great
skills and experience to observe it.
- One can say, that once You got a diffuse discharge, then install it between two aligned
mirrors and it will lase. It is a heavy delusion. First You need a proper gas mixture. Among
all possible ones only a few are usable. Then You need a huge current through Your discharge.
The discharge glow may seem acceptable but low current means low gain and Your laser may
even not reach the threshold. Third is the correct pressure (dependent to mixure contents
of course.) If Your laser seems to work at any pressure, it seems it does not work at all.
(You may observe some disturbances instead of laser signal.)
The problem has too many parameters to vary for one person could solve it. Even a deep
theoretical study wont help much. (Try to analyse the conditions of volumetic discharge in
electronegative gases for an exercize.) So keep close to one known solution and vary a
little for a time.
- The electric pulse source of the laser has a simple schematics. It just produces a
fast rising heavy current pulse by fast discharging the capacitors. It may seem that several
other schemes are equivalent. They arn't. Refer to fig 27 to see.
"Figure 27. Working and not working schemes of power supply."
When powered by scheme of figure 27a the volumetic discharge glows in wide range of pressures
and only with heavily worn out electrodes there appear some sparking. Usage of fig 27b scheme
leads to narrower acceptable pressure range and the discharge becomes more sensitive to
the state of the electrodes. At last, when testing with the fig 27c scheme, it is almost
impossible to get the diffuse discharge even at very low pressures for this laser
(till about 20 Torr).
- Always pay attention to the inductance of wiring. This laser is not so critical as its
nitrogen brother, but the lower inductance is the better. When electrodes are connected only
by their endings (as it was shown on pictures above) only short samples of the laser are
operational. When designing a long one, dont shy to add as many contact belts as You feel
necessary.
- The laser has two modes of operation: "High Power" and "High Energy". The boundary between
the modes is of course rather conditional and one mode smoothly flows to another when changing
parameters.
Typically the High Power mode takes place at high pressure (generally above 100 Torr) with
high (but not excessive) CO2 concentration. When in this mode the laser beam makes glowing
spot on all absorbtive surfaces. It is not very bright but can be clearly seen at daylight.
When far from laser (when not interfered by its noise) one can crearly hear flicks when
beam hits the surface. The power meter reading is not maximal in this mode however.
With lowering pressure at first the energy and the power vary only a little. The gain is also
almost stable. After reaching some boundary (usually below 100 Torr) the gain and the output
energy begin to rise. At the same time the peak power drops down. Laser enters the High Energy
mode. At a certain pressure point the output energy reading becomes maximal (about twice
of the one in High Power mode) but the beam now does not produce glowing spots and other
high power phenomena. The energy is really maximal here - You can ensure in it by drilling
some plastic plate, it will be considerably faster than in High Power mode.
With further pressure lowering the output power drops gradually until it becomes under the
measurement errors.
The exact values of pressures corresponent to energy peak and to power peak depend to
gas mixture contents and even to laser assemblage details (e.g. it depends to preionizer
assemblage quality) so You will need to find them out yourself (and dont forget to write
them down - You will refer to them later frequently)
- With a proper external power supply the laser is capable to work in QCW mode. It was tested
at repetition rates up to 10 Hz without any noticeable power drop. No external coolant was
used. It was even able to operate in QCW mode while being quasi-sealed off (both valves shut
up). After 15 minutes of operation at 10 Hz no considerable power loss was noted. It is rather
strange since co2:air mixture was used and there were all conditions for nitrogen oxides
accumulation. It seems like the excessive gas volume in the tube helps it to lase for so long
time.
- This photo shows a TEA laser, similar to the one that was described in a guide here, but
having polyethylene intracavity window and metal covered output mirror with 3 mm coupling hole.
It appears that usage of polyethylene window reduces the laser output nearly twice. Usage
of drilled mirror halves output once more. However even this shrinked output (about 15 mJ)
is quite enough to produce many interesting things. Parameters of the laser are the next:
Cathode width 15 mm, anode width 20 mm, discharge column with 8 mm. Length of the electrodes 40 cm.
Storage bank - 10 capacitors, 4700 pf each. Charging voltage 10 kV
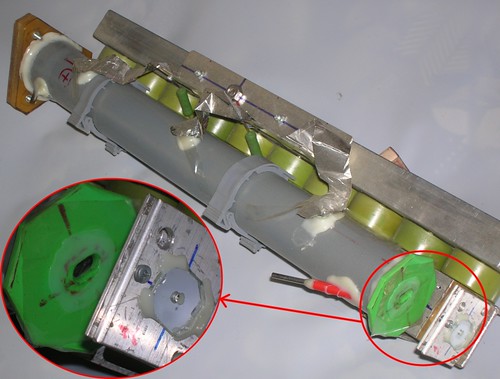
<< HOME PAGE |