If You are planning to build a laser, acceleration tube, electromagnetic interference
generator or something else of this type, sooner or later You will meet the need to use
a high voltage low inductance capacitor, that only can deliver the necessary gigawatts
of power.
In principle You can try to avoid hand work and use a ready capacitor. Luckily the
market contains something like one You need. Those are doorknob capacitors KVI-3, K15-4,
a number of types are produced by Murata and TDK, and certainly the so called
'monster-capacitor' of Maxwell 37661 type (the last one is not doorknob however)
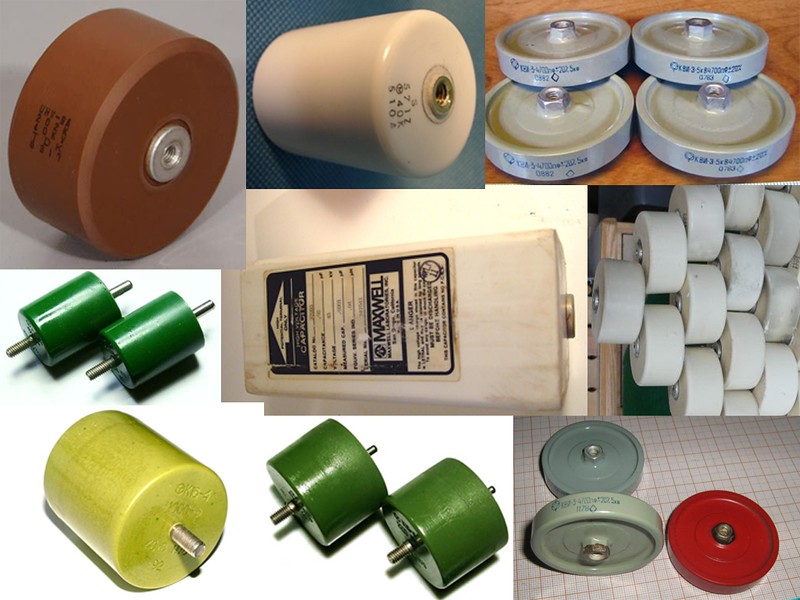
However the usage of ready made capacitors has its own drawbacks.
- It is expensive.
- Those capacitors are hard to get (The Internet certainly has bound people, but
it bugs to scavenge junky parts from the other side of the Earth planet)
- And the most important: At the very end those capacitors will still not provide
the record parameters that You want from them. (When we speak about ten or even less
nanosecond discharge time for nitrogen laser pump or for getting a beam of escaping
electrons from not evacuated acceleration tube, this cannot be done by any Maxwell)
Following this guide we will learn how to build a handmade low inductance high voltage
capacitor. In this example the board being described is intended for use as a lamp
driver for dye laser. However the principle is common, so one can implement it for
his own needs, including (and not limited by) the nitrogen laser.
I. RESOURCES
↑
- some plastic pieces of suitable size, these ones will be used as top and bottom
boards of the capacitor (kinda box);
- some pieces of aluminium angle or U-shape, these ones are used as high-current
leads;
- laminating pouches

When buying a box of laminating pouches read carefully the small font text on
the box covering. If You find words 'nylon' or 'polyester' feel free to purchase
- - this is the legendary mylar - the most high-voltage material among reachable
for DIYer ones. If there are no such words it still probably mylar (due to the
fact that it is hard to make temperature endurable pouches with something else)
but there are no warranties.
For the voltages |
choose the thickness of pouche at |
up to 10 kV |
60..80 mcm |
10..15 kv |
100 mcm |
20..25 kv |
150 mcm |
25..32 kv |
200 mcm |
When working with voltages above 35 kV and up to 50 kV - choose the most thick
(200 mcm) pouches and don't forget to add extra insulation layers when assembling
the capacitor.
Don't try to make a capacitor for more than 50 kV - the auto emission from thin
foil edges will make it senseless to add more insulation. Here You will need either
to use a metal plate of noticeable thickness as a foil of the capacitor, or use
series connection of several capacitors, or make a Marx bank generator.
- household aluminium foil
For understandable (from the previous paragraph) reasons the thicker is foil the
better. Thick foil lets the capacitor to operate more stable and endure higher
voltages. On the contrary the industry continues to learn how to make the foil
thinner and thinner and forces people to consider that 6 mcm is quite enough to
put a fried chicken in. The most thick aluminium foil that can be now found in
food stores have 16 mcm thickness and bears the prideful name "extrahigh tensile".
Exactly this one we will use for our capacitor. If You have more thick industrial
foil handy - good for You.
- office laminator machine
The main requirement it that it must be able to work with chosen size and thickness
of laminating pouches.

- You should have other misc tools and fittings.
II. ASSEMBLAGE
↑
When designing a device that requires low inductance feeding, one should think
about the whole unit rather than about its parts separately (e.g. separate capacitors,
separate laser head, etc). If not, the advantages of low inductance of the capacitors
may be easily eaten by connection wires. Usually the capacitors are the organic
part of the whole device. That is why this guide shows dye laser driver circuit
rather than capacitors separately.
The one DIY'er is blessed, who has foils of fiberglass plastic and perspex plates
lying around. Others use what they can get. (E.g. kitchen butcher board.)
So get the piece of plastic and cut it into the size of future circuit.

The circuit is primitive. It has two capacitors (the storage one and the peaking one)
bound together by spark gap to form a charge transfer circuit. Here we are not intend
to dig through circuit operation details, we are to study the design of the capacitors.

When You have chosen the size of future capacitors, cut the pieces of aluminium
angle to fit the sizes of future capacitor leads. Process the leads according to
all rules of high-voltage technique (round all edges).

Then fix the capacitor leads on the 'printed circuit board' being made.

Mount all parts of the circuit that could interfere with capacitors assemblage.
In our case those are connective buses and the spark gap.

Please note that low inductance of the spark gap mounting is sacrificed to
the affordability of its adjustments making. It is reasonable here due to the fact
that according to the black body law the lamp won't emit light faster than
sigma*T^4 with even a driver circuit of infinite speed. You can only shorten
the risetime but not the full width of the pulse. On the other hand, when
building e.g. nitrogen laser, You will not have so free will when attaching
the discharger.
The next stage is to cut the aluminium foil into pieces of suitable size and
shape, and possibly to do the same procedure with laminating pouches (it isn't
needed if your capacitor was designed for utilizing of full size of laminating
pouches, as it is here with storage capacitor.)

In spite of the fact that ideal laminating gives vacuum-tight boundary and
the there should not be any flashovers around the edges, one should not
leave rims (size d on the picture) less than 5 mm per each 10 kV of applied
voltage. Rims of 15 mm per each 10 kv allow the capacitor to operate
reasonably well even without being glued tightly.
The size of terminals (size D on the picture) should be chosen equal to
the proposed thickness of the future stack with a reasonable reserve.
Corners of the foil should certainly be rounded.
Let's start with peaking capacitor. Here are how the billet and the
complete (havin been laminated) foils do look like.

The peaking capacitor uses 200 mcm laminate due to the fact that voltages
up to 30 kV are expected here during charge transfer process. The necessary
number of foil is to be laminated (in our case 20 pcs). When ready
stack them one upon another (putting their terminals in turn to the opposite
sides). When stacked, bend the terminals gently. (The obtained stack may
require some cutting of the excessive foil at the terminals.) Put the stack
into the nest, formed by leads on the circuit board. Compress the stack with
the upper cover.


Good boys will fix the upper cover with nice screws, but it can be done
even with a duct tape. At last peaker capacitor is ready.

Assemblage of energy storage capacitor is similar to the work already done.
Less scissor work because here we use full A4 format. The laminate pouches
here are chosen with 100 mcm thickness, since 12 kV charging voltage is
planned.
As above we stack foils, bend terminals and compress with covering.


The kitchen board with milled handle looks evil, but functionality is kept.
I hope that You have less problems with resources. One more thing to note:
If You are planning to use some wood as a basement and covering, You should
prepare it accordingly. You should dry it well (preferably at high
temperature) and then varnish it tightly (use yacht or vynil varnish).
The issue is not dielectric strength or leakages. The point is that when
humidity changes the wooden parts do bend. At least it weakens the contact
and hereby slowers the discharge. Moreover if You plan to attach a laser
above this board the board will bend it too, with all following consequences.
When bending leads feel free to put additional (border) layers of dielectric.
Or else it happens that capacitor plates are separated from one another by two layers
of laminate, and leads are separated from an opposite polarity plate only by one layer.
If You forgot to add those layers the capacitor will remind You to do so as soon as
You turn it on.
Let's see what we have. Use a multimeter with capacity measurement abilities.
Here's what the storage capacitor shows.

And here is readings when peaking capacitor is attached.
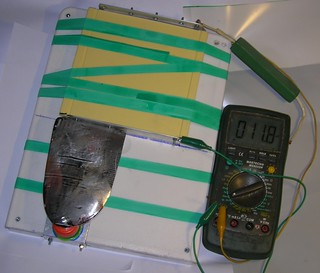
Generally that's all. Capacitors are ready and the theme of the guide is
finished. However it's probably interesting to test the capacitors in action.
After finalizing the missing parts of the circuit all that left is to put
the lamp in its place and to attach to the suitable power source.
This is how it looks like.

Here is a trace, obtained with a small wire ring being attached directly to
an oscillograph and set up near the lamp feeding circuit. (However this one
is taken with wire shunt instead of lamp)

And here is a trace of the lamp light, obtained by fast photodiode faced
to nearest room wall. The diffuse light is quite enough to see what happens. "More than enough" - that would be more correct.

One may blame the capacitors and seek for what has gone wrong, and why the
pulse is longer than 5 microseconds... until remembers about the photodiode
saturation. Let's set the photodiode further away. Here is a trace when the
photodiode is placed at 6 meters from the lamp and is faced not directly to
the lamp but rather slightly inclined.

The risetime is not traced precisely due to pickup, but one can estimate it
to be about 100 ns. That is also in accordance to the duration
of current pulse half-period.
Other part of the light pulse is the glow of slow cooling plasma, giving full
length at about 1 mcs.
Is it enough for dye laser? This is a separate question. Usually such a pulse
is more than suitable. But in practice it strongly depends to type and purity
of the dye, to type and purity of the solvent and to denials of laser cell and
laser cavity design. If I succeed to lase one of available fluorescent markers
then here will be a separate guide on this laser. If not it's senseless, because
chemicals (organic dyes particularly) aren't freely available for DIYer's.
As for this circuit I am pretty satisfied with the discharge time but I am
not satisfied with voltage (the board has failed to light a 15 cm long quartz
xenon flashlamp) and energy. So I am going to replace the spark gap by more
high voltage modification, and add some plates to the storage capacitor
(about the same quantity as already done.)
(PS) I did so and the board has proved itself to be really able to drive dye laser.
The tube (its image You can find on this site in Misc Photos section) works
with this board even better than with two-maxwell Marx bank
Generally the 100 ns discharge time is not the limit for capacitors built
following the described technique. Here is a photo of capacitor, capable to
drive a low pressure air-nitrogen laser to superradiation.

Its discharge time is below my oscillograph capabilities, but the fact that
nitrogen laser oscillates perfectly already at pressures of 100 Torr allows
to estimate the discharge time as being below 20 ns.
III. INSTEAD OF CONCLUSION. SAFETY
↑
To say that this capacitor is dangerous is to say nothing. It is almost as
lethal as a trailer rushing at a speed of 100 mph towards You! You should
fear it and respect it as You fear and respect weapons! Use all means of safety,
including turning on and off from a safe distance.
It is impossible to foresee all dangers and to describe what to do and what
not to do. Do You know when sapper career ends? Exactly when he stops to fear
and begins to be familiar with explosives. At this very moment it blows his head away.
So be careful.
However millions of people drive cars and thousands of sappers work with
explosives and stay alive. When You are careful enough all will be ok.
Shirt type capacitor
↑
This capacitor type gets its name from the similarity of its foils shape and a shirt.
The inductance of this capacitor is greater than of the capacitor described above or the candy type one, but it is still usable for CO2 laser or Marx bank generator. Barely drives a flashlamp dye laser lasing and being completely useless for N2 laser (except maybe some very special cases).
Materials needed are the same as in the guide above: mylar foil (or laminating pouches), aluminum foil, electrical tape.
The drawing below shows the dimensions of the main indents.

L - length of the dielectric
D - width of the dielectric
R - outer radius of the capacitor
Indents along the edges of the dielectric are 15mm each. The side through which the contact terminal goes has the indent of 50mm. These indents are made as minimal as possible for maximum capacity when having existing L and D dielectric dimensions, note that they are specially chosen for 10kV (I doubt that there is any sense to make such type of a capacitor for any higher voltage, so I won't put here the relations how to calculate the indents for them).
The top foil (the one that will face the inside when wrapping) is shorter by some length than the lower foil. It is needed to compensate the shift of the layers in the process of winding. This excessive length can be calculated by the formula:
= 2*pi*n*( +x) or = L*( +x)/<R>
where:
x - foil thickness;
- dielectric thickness;
n - number of turns;
<R> - average winding radius(the arithmetical mean of the outer and inner radius).

For example for the capacitor described below: =0.125mm; x=0.02mm; L=300mm; <R>=4.5mm.
Then =300*(0.125+0.02)/4.5=9.66mm - i.e. approximately 10mm.
To estimate <R> You can try to make a few test turns without foil.
The spacing between the inner borders of the contact terminals - 30mm. It is also taken as minimal as possible for 10kV. The increasing of the gap will make the terminals too narrow - the capacitor inductance will then be increased.
Production
↑
- Take a pair of mylar sheet (A4 format) or one pouch for laminating. Make sure that the dielectric thickness is well above 100 mcm (125 or 150 mcm serve well)

If you are using a dielectric sheet, cut a sheet of twice the size, and fold it in half, as shown below.

- Use some nonconductive drawing tool (NOT A PENCIL!) to make markup on the dielectric. Indents: 50mm from the open side (the side where the terminals will go); and 15mm - at all other edges.

- Cut the first foil electrode of the capacitor according to the scheme below. Dimensions are taken based on the size L and D of the dielectric (when making a narrower part of the shape that will be used as the capacitor terminal later feel free to use a large excess of length. It is good if You can wrap the terminals around the capacitor body for several turns):

In the photo it looks like this:

- Cut the second foil electrode of the capacitor according to the scheme below. Dimensions are taken based on the size L and D of the dielectric:

The photo below shows the foils laid one onto another - for You to see the difference of their sizes:

- Insert the first foil (the one with larger main part) between the mylar sheets (or into the pouch if You re using them). Use the markup to position the foil correctly.

- Put the second foil on top of the "sandwich" as shown on the photo below. You got something what looks like a shirt.

- Along the edge that will be the internal after wrapping (the one opposite to the side with terminals) cover the second foil with some adhesive tape. There s no need to glue anything else.

- Wrap this "sandwich" as tightly as possible. It is good to start the wrapping from the end opposite to the one with terminals. Ok, boys You really could try to wrap it beginning FROM THE TERMINALS and it is really interesting what You will get in the result ( however the thing You get in this case would have nothing common with a capacitor.) Fix the capacitor just having been wrapped with some sticky tape.

- Tighten the contact terminals. Wrap the capacitor with adhesive tape. Leave free only the contact terminals.

- Measure capacity. And make sure that the desired received.
ATTENTION: before poking capacitor with a multimeter, make sure that the capacitor is discharged, even if the capacitor has never been charged (it could got a charge from static).

Shirt type capacitor is ready to use. You can install it in your laser, Marx bank generator or other high voltage device.
<< HOME PAGE
|