Many lances were broken on the topic of a cheap and affordable vacuum pump. People use the reversed fridge compressors, water jet sucktors and so on. The first are bulk and heavy, the last give water vapours in the volume being sucked, and also require tap water nearby.
Besides that there exist at least one elegant solution affordable almost to anyone and free from most drawbacks. We shall use a cheap automotive tyre compressor.
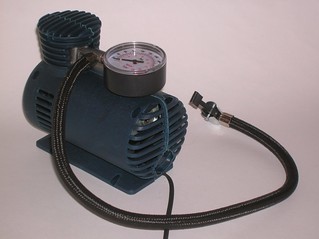
Here it is. It costs about 10 bucks. Beware not use more advanced ones - most pobably they use too special manifold system to rework it at home. Those china cheap compressors can be found in supermarkets in departments of auxiliary products.
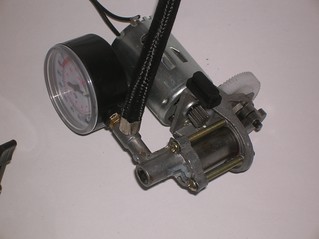
This is how the naked pump looks like after its plastic housing has been removed.
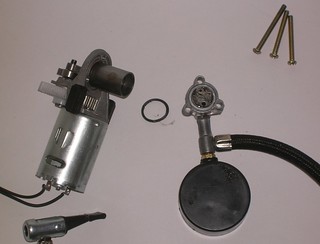
The pump's cylinder has manifold head above. We should remove the head to work with it.
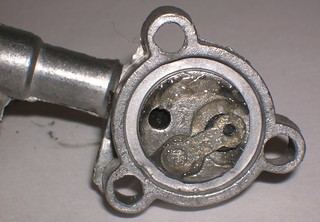
On the left image this strange and humble looking plug with hexagonal pit for the screwdriver appears to be the output valve.
The right image shows the intake valve. This one is made from rubber stopper. Other variants of the compressor may have flap valves made of steel or platic. They look similar but there's no rubber stopper beneath the flap, and the flap is elastic.
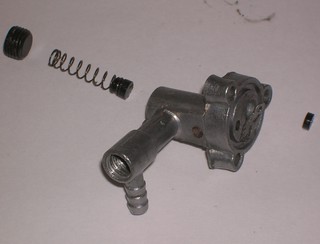
We will use heat for further operation. So it is a good idea to remove any non metal parts from the manifold head.
Attention: if your compressor has a flapping type valve don't bend it. If You behave too hard with it it may stop to open or to close so just try to leave it alone.
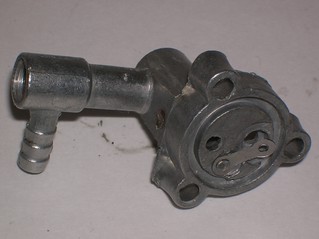
The main body of the manifold head is needed to be clean and degreased. Put the part into a vessel filled with clean (solvent grade) petrol and stir it there. Then dry the head and discard the petrol safely.
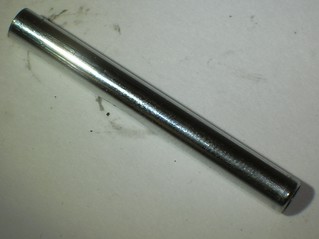
Get a hose (metal tubing of proper length and diameter). It is handy to use a part of telescopic antenna pipe. However You may have better resources. Choose the diameter of the hose according to your vacuum pipes. (In case of PVC aquarium pipe it will be around 5 mm).
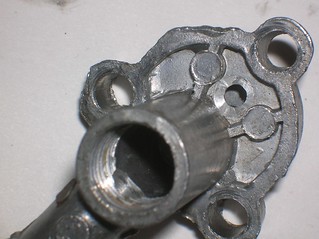
Drill a small pit in place where the hose will connect with the head. Use the drill with the same diameter as the hose. Try not to drill throughout.
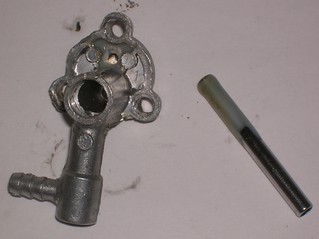
Put some hot glue (glue gun rods) onto the place of future connections. Heat the metal with propane torch. Stir for the hot glue to distribute evenly over the parts surfaces. Take care for the glue not to sneak to the valve - it will kill it.
Attention: if Your pump has flap type valve heat the head with extreme care - you may temper the steel and it will loose the elasticity.
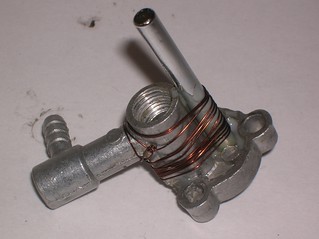
Wrap the hose to the head with some wire. And press for the tube to go into the previously drilled pit.
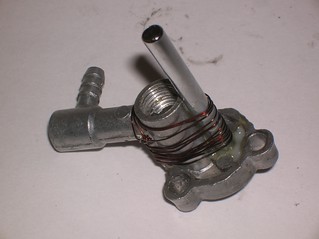
Heat both parts in place of connection to glue up. Add the hot glue according to Your taste.
Again keep the glue from sneaking into the valve.
Cool the parts and then You may start the reassembling the pump.
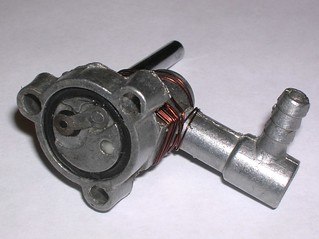
Install the valves into their places. You may try to lubricate the valves if You are knowing what are You doing, however improper lubricant or improper amount will result in bad vacuum.
Another good idea is to tune the gap in the intake valve. If it is pressed to its saddle too strong it will open only at too high pressure difference - bad vacuum result. On the other hand if the gap is too large the flap may close too late resulting in back air flow.
Attention: flap type valves are usually easy to break, so it may be better to leave them alone.
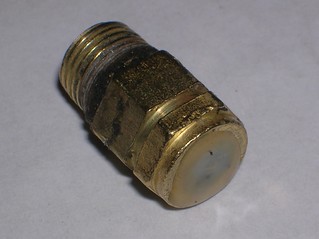
The manometer in those pumps has poor quality. Forget the idea to refurbish it to make a vacuumeter. So You may use the hose of this device as a plug.

The pump havin been assembled back.
Before assemblage one may want to lubricate the piston and the crank gear.
If needed one may put the pump into its native housing or make other attachment means. E.g. as at the picture below.
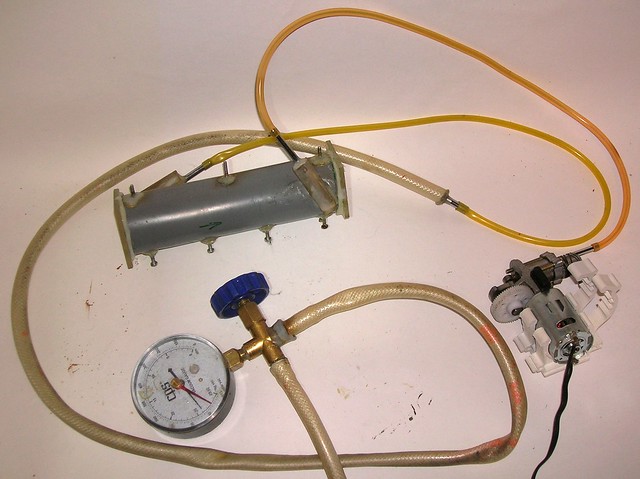
Here is how it works. As You can see this humble device can hit the pressure of 1/10 bar - almost the same value as the bulky fridge compressor does.
Addition
Also there were produced two more species with different types of inlet valves:
- Pump with a metal lamellar valve.
|
|
- Pump with a plastic lamellar valve.
|
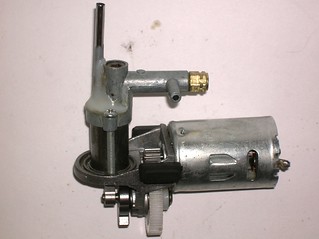 |
|
 |
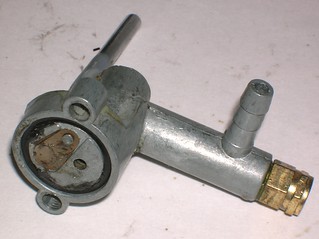 |
|
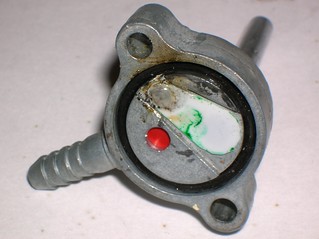 |
* Metal valve is definitely more reliable and lives longer. But it has less elasticity. |
|
* In fact this thing also had a metal flap as a valve. But it was contaminated with glue, and there was no success in its cleaning. The only way to revive the pump was to make the new valve from a piece of mylar. It appears to give a very good results but no one knows how long it will live. |
Conclusion: if the resulting pump does not suck well, you can try to boost it by installing more flexible inlet valve. However there's always a good chance to mar the thing.
As an example: the photo demonstrates the functionality of a low pressures nitrogen laser evacuated by the pump having plastic flap valve.
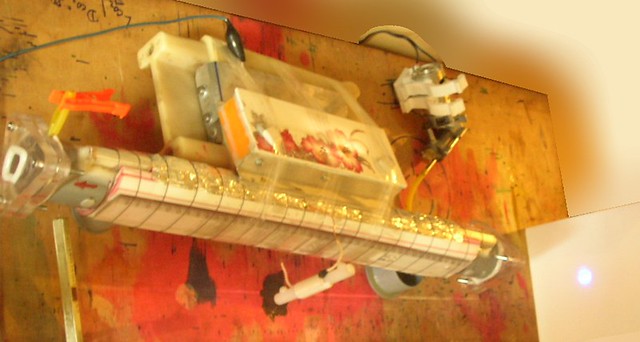
<< HOME PAGE
|