|
When Nickola Tesla was asked,
which of his inventions
was his most favourite one?
He answered: "My turbine"
|
Here we will r_a_p_e the idea of gas turbine complicatedness. Don't expect
to see a large and usefull engine here. Its just a model, kinda alike those
tin can Stirling engines, filling the net media.
SO WHY?
It is said that a turbojet is extremely hard to make at home. So
hard that only one human on the Earth was able to do that (Some Deutch guy,
namely Shreckling) and any other successfull homemade turbines are just
reproduction of his design. (For me it looks just like an importunate
advertisment, but You still can find such a statement in many places over the
internet.) Others say that it is hard even to obain a self sustained mode of
operation. (One can easily find the proof of this in comments on YouTube. -
Almost any homemade turbine build is accused of being non self sustainable.)
Besides the basic idea of gas turbine engine is one of the most simple in the
world. It has no cylinders, no pistons, no crank, and no timing valves. It has
only one moving part (the shaft with turbine and compressor wheels) and even
its motion is just rotation.
The only difficulty is that turbines are thought to have very high revolution
rates. People got used to numbers like 70 000 rpm or more when speaking about
gas turbines. Indeed, at those revs one needs a carefull design, strong
materials, high precisions and so on.
Any book, analyzing Brayton cycle or gas turbine operation, eventually comes
to the conclusion that there is no rpm threshold due to gas dynamic or
thermodynamic properties. The need for the high rpm arises only from the
necessity to overcome friction. And if we could keep it low enough...
SO HOW?
Three key principles are the next:
- The turbine should be larger than the compressor. This provides that turbine
driving torque is higher than the compressor braking torque in tremendously
wide range of conditions including the lowest possible efficiencies.
- The gas flow from the compressor to the turbine should not be choked. There
should be no waists in the path. Moreover, because the gas tends to expand
when being heated in the combustion chamber, the constant section flow path
can also be treated as "waist". In order to avoid this the flow channel
should actually be widening. And the area of its section at the approach to
the turbine should be K times larger, than the area of its section near the
compressor. The K ratio should be slightly less than the ratio of the exhaust
temperature to the inlet temperature. (Absolute temperatures are meant.)
Slightly less - for some flow acceleration, but not too much - to avoid
risk of choking. The good initial approximation: K=2..2.5.
- And finally the friction should be as low as possible. The wide spread
solution - to use an old bike axle in place of shaft and bearings won't suit
if we want to keep rpm not higher than 1..2 thousands. Another old good
solution - the use of pinpoint bearings (pin-to-pit support) - have proven
itself to give fairly good results (from any point of view but reliability).
Three additional principles are not the key, but You should attend them to
make the life easier:
- The turbine blades are set as so the angle between them and the axis of
rotation is 1.2 radians. It corresponds to the angle between the blade plane
and the turbine wheel blade equal to 21 degree. The optimal angle depends to
the behaviour of Lift to Drag ratio for the particular blade profile, You get
when curving the blades of Your turbine. A planar blade reaches a reasonable
(I got 80% by numeric calculations in the inviscous flow.) efficiency for the
angle mentioned above. And it tends to grow for smaller angles (between the
wheel plane and the blade plane). On the other hand, too shallow angle means
too low torque, so here is the subject for compromise.
- The angle of compressor rotor blades was found to be good when in range from
30 to 45 degrees (again between the wheel plane and the blade plane). At
lower angles the turbine tends to attain higher rpm and power, but harder to
start. At higher angles the engine starts more easily (sometimes self-start
is possiple when the tip bearings and balance are good enough), but the
top achievable rpm and power are lower.
- As we are trying to set no obstacles in the flow path there are no stators.
In the conventional turbojet the first stator rectifies the flow and forces
its energy to become pressure. After the combustion chamber the last (second)
stator spins the flow again. And in the same direction as it was rotating
after leaving the compressor. So why not to let the flow to spin freely and
to deliver the torsion energy just back to the shaft by driving the turbine?
The design is clear from the pictures below.

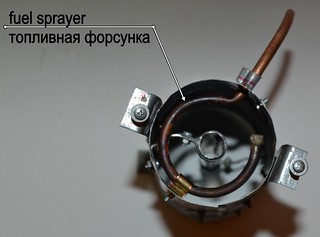

The shaft is made of a 5 mm taping arrow. The wheels are cut from a can metal
(thin steel plate). Their blades are cut and then turned by pliers. I tried to
apply some wing-like curvature to the blades and succeeded... to some extent.
The depth of camber is 3 mm for the turbine blades and 1 mm for the compressor
ones. Compressor has 65 mm diameter, turbine has 95 mm diameter.
Since the taping arrow appeared to be unable to be hardened, the pins were
made of some drill bit pieces. The pieces were annealed, then sharpended, then
hardened again. Then they were installed into the specially foreseen holes at
the ends of the shaft.
The casing is made of can metal (spotwelded). At the ends of the casing there
are two straddles, with shaft keeping bolts. The bolts have pits that can hold
the pins of the shaft. The bolts are needed for fine tuning of the device.
The casing also contains a shaft screening tube - just a piece of a steel tube,
placed along the axis of the device. The tube is needed to prevent overheat of
the shaft. (which will be red hot in less than 30 seconds if not screened.) The
engine operates successfully even without the screening tube, but in a short
time it fails due to the shaft bending.
The thing is fed with propane gas from an LPG tank equipped with a pressure
regulator. The fuel sprayer is a ring of copper pipe, carrying four orifices,
each 0.5 mm in diameter.
Starter is any suitable fan. No need to have a powerfull one. Correctly built
and finely tuned engine can be started from an average computer cooler.
Ignition system is any suitable butane blowtorch. Just open the fuel flow
and fire the gases at the turbine exhaust end. At some point the flame will
blowback into the combustion chamber and no more external ignition will be
longer needed.
It works and it is pretty self-sustained. What else did You want for the price?
<< HOME PAGE |