There exists an opinion, that the best way to deliver the radiation from
laser lamp to laser rod is to put the lamp and the rod into foci of glossy
elliptic reflector. It is assumed here, that the lamp and the rod are straight,
and the "elliptic" reflector is naturally a cut of elliptic cylinder. Obviously
its "foci" are not single points, but straight lines, so the rod and the lamp
are to be "put onto" these lines.
In reality the expression, that says that the usage of elliptical reflector
is the way to the topmost efficiency of lamp pumped laser, is at least
questionable. Maybe so it is in pure theory (however I doubt that anybody has
really performed a full scale variational analysis, intended to find the most
optimal variant from all the functions, that describe the shape of the
reflecting surface with taking into account non zero radii of lamp and rod),
but the practice gives the evidence that it is not correct. For example, the
classic closely coupled reflector (lamp being wrapped to the rod with some
reflecting foil) in most cases works better. And one needs to apply serious
efforts, in order for the elliptic reflector to give the results at least
comparable with the ones of the tightly coupled one.
Then why to pay more? If we have an old good closely coupled reflector,
why one should try to use a complicated elliptic one, with also an indefinite
perspectives concerning the improvement of laser yield?
The reason is just here. The elliptic reflector is the most direct (and maybe
the most efficient) way to take apart the laser lamp and the laser rod. For
they not to rub their hips with each other. In its own turn it is needed for:
- Preserve the laser rod in case of lamp explosion. If lamp exploded in the
close coupling, the rod will certainly die. On the contrary if the rod and
lamp were placed in elliptic reflector, the chances for the rod to survive
are considerably higher.
- To separate the rod and the lamp in terms of heat. Indeed even xenon lamps
have poor efficiency of electricity to light conversion. More than a half
of the supply energy goes directly to heat (ohmic heating). If the lamp
is in physical contact with the rod, it begins to use it just as a heatsink.
In its own turn this can cause overheat of the rod, and, in the worst case,
its thermal crackling.
- To separate the rod and the lamp in terms of mechanical loads. Instant
deposition of heat on the lamp is essentially a small explosion. With all
its consequences such as vibrations, stresses and shockwaves. When these
stresses reach the laser rod, they are more than able to cause a negative
influence onto the lasing. For example in practice of liquid lasers it is
well known, that lasing can stop not when the pump power goes under
threshold level or when some waste products has accumulated, but rather than
that when the acoustic wave reaches the cell with laser liquid and shocks it
so strong, that gradients of refractivity make the resonator to become
misaligned.
So, how exactly to build the very elliptic reflector?
Here are a few variants:
-
One can take a disc mill, install it at a slant and mill a chase in a solid
material

Since a projection of a circular trajectory of the mill's teeth onto the
plane of drawing is ellipse, it means that the resulting shape is
mathematically correct elliptic cylinder with the precision to the wobbling
of the tool and to the errors of the bench. Further on one needs only to
polish the surface (and maybe to cover it with some reflecting coating).
For the correct placement of lamp and rod one should also know the positions
of the focal lines. However this problem is easy to solve if one knows
the lengths of the axes of the ellipse (the one, which is the cross section
of the elliptic cylinder). Then one can use a simple math formulae:
c = sqrt(a^2 - b^2), where a - semi major axis, b - semi minor axis, c - is
a half of the distance between the foci. (Remember also that the foci
are situated on the major axis and they are placed symmetrically in relation
to the center of the ellipse. With this information in addition to the value
of c, it is more than enough to determine the correct position of the foci.)
One can take a common (round) tube (made of some high reflective material:
copper, brass, aluminum, or even silver), and plastic deform it in vise.
Then polish:

Similarly to the previous case the formulae c = sqrt(a^2 - b^2) will help
You to determine the positions of the foci (note that 'sqrt' means square
root). a and b are the lengths of major and minor semiaxes of the shape,
measured after the reflector have been taken out of the vise.
One can take a CNC machine and order it to make a proper elliptic shape
with necessary parameters. In addition the machine will easily make the
endcaps, with the holes for the rod and the lamp positioned exactly on
the focal lines of the reflector.
The drawback of the first method is obvious. One needs a milling machine.
And it is not affordable easily to anyone.
The drawback of the second method is that the resulting shape differs
seriously from a mathematically correct elliptic cylinder. However it may
be amazing, but mathematically correct elliptic cylinder proposes not much
of gain in comparison to the reflector, having been made by this way. Most
of amateur failures with this type of the reflector are not due to bad
focusing, but due to bad general design (more details on that see below).
Considering the this variant, it could be completely not worth of
attention (well, where are we to get a CNC machine if we have no simple
milling one?) if not for 3D printing. Indeed my Proxxon engraver, being used
widely in all my projects, is not cheaper, but MORE EXPENSIVE than most
of budget models of 3D-printers. Many people are trying to avoid risks of
buying 3D-printer, because they treat it as a useless toy (in comparison
for example with that Proxxon again). And indeed such an impression can
be easily formed when one looks at those clumsy figurines, that are almost
everywhere in the Internet are shown as the results of 3D-printing. However
this impression is just... wrong. 3D printer, even a budget one, is a serious
help for many DIY projects. And if You haven't yet got one - I recommend You
to bother.
Before rush to mar plastic or metal, one should calculate or design the
elliptic reflector properly. What does it mean in practice?
One of the very common problems - is to diverse the lamp and the rod by
known amount of millimeters without exceeding some pre-known size. It is
a simple task: if h - is the required spacing between lamp and rod surfaces,
the necessary distance between rod and lamp centers will be h+r1+r2, where
r1 and r2 are radii of the lamp and of the rod correspondently. Further note,
that the distance between rod and lamp axes is the distance between focal
lines. I.e. 2c = h+r1+r2. The maximal size of the ellipse is determined by
its major axis (2a). Then using the formulae b=sqrt(a^2-c^2) one can obtain
the lacking size, and go draw the reflector.
More complicated is the task, how to smash a tube of known diameter to such
extent, that the distance between focal lines would be equal to some needed
value? In order to solve this task remember, that the perimeter (circumference)
of the circle won't be changed during smashing. It means that among all the
ellipses, that have their perimeter equal to the circumference of the initial
tube, one needs to choose the one, that has the distance between its foci
equal to the needed one. The problem is far more complicated than typical
school ones. If it is difficult for You to solve it by Yourselves, use the
help of
In the upper right corner of its working window there is an auxiliary tool -
a frame of a program, that calculates two unknown parameters of an ellipse
by using two known ones. (There are totally four of them: a - major semiaxis,
b - minor semiaxis, c - half of the distance between foci, p - perimeter.)
In the fields of input set the parameters to be find to zero. Enter two other
parameters and push the button "calculate". The picture above shows the
tool frame as being outlined by red dotted line and aimed on by red arrow.
Enter the circumference of the tube (section) into the field p and enter
the necessary half distance between the foci into the field c. Press
"calculate" and receive the information about a and b. (Note however, that
if c is too high, the perimeter may be barely not enough for the task to be
solvable.) Further on, one can go smash the tube in vise, trying to get
proper sizes of ellipse axes.
Even more complicated task is: if the distance between foci 2*c is known,
radii of lamp and rod r1 and r2 are known, and the reflectance of the reflector
coating is known too, then how to choose the sizes of ellipse a and b, for
the effectiveness of the light transmission from lamp to rod be not less than
some known level? This goal can also be helped by the "elliptic reflectors
calculator" utility, but now one should use its main window. Despite its simple
view, it is a full scale 3D raytracer. It is obvious, that the sizes of lamp,
rod, and elliptic reflector can be entered in any units (inches, millimeters,
furlongs, etc). It is only essential that You keep the chosen system of units
in all calculations. After You have succeeded to enter all the values without
errors, and have pushed the button "OK" and then "Raytrace", You will get the
next picture:

The value of most importance for You here will be the amount of the lamp
light, that have succeeded to reach the laser rod (outlined by red dotted line
and pointed by red arrow). This value is given in absolute units (in number
of rays having been emitted by the source) and in percents. These percents
are essentially the effectiveness of Your chosen reflector in relation to
the transmission of the light from the lamp of chosen diameter to the
rod of chosen diameter.
Those are the calculations. They can estimate the efficiency of the chosen
variant of the reflector, but they can not optimize all the parameters for
You. How to do it manually? It is usually taken, that for the best efficiency
the lamp and rod are to be as close to each other as possible, and the radii
of the lamp and of the rod should be negligible in comparison to the smallest
axis of the ellipse. Moreover, the higher is the ratio of the axis to the lamp
or rod diameter, the better. This choice of geometry leads to the fact, that
major and minor axes of the ellipse become almost equal to each other, and the
ellipse itself becomes more like circle. It even becomes possible to treat this
ellipse like circle of some "mean" diameter - the average between major and
minor axes.
However who needs such recommendations? To place the rod as close as possible
to the lamp? - There is close coupling for this. And we use the elliptic
reflector exactly for the opposing - to diverse the lamp and the rod from each
other.
To increase the mean diameter of the reflector? But then the light losses to
the ends of the reflector increase drastically. It lowers the overall
efficiency. And the lamp and the rod in reality never have enough length to
neglect that losses.
What else could be recommended? To my opinion there is no general
recommendations here, acceptable from the practical point of view. Try to
vary the ratio of the ellipse axes to the lamp and rod sizes, and to the
spacing between them until the result will be acceptable for You. Keep in
mind, however that the ideal is unreachable. Seek for the tradeoff.
Most cheerfully the efficiency of laser reacts on the ratio of the diameter
of laser rod to the diameter of lamp. The thicker rod and thinner lamp - the
better. Do note, that You are unable to choose to thin lamp - You will loose
the allowed pumping energy and may become unable to reach threshold. In the
practice if the rod is by twenty percent thicker than the lamp it is good.
If the rod is 1.5 times thicker - it is excellent.
The next thing, that efficiency of laser depends on strongly - is the
reflectivity of the reflector coating. It is rather strange, because it is
usually taken, that the light wanders freely from side to side in close
coupling fixture (light oven), and in the elliptic one it undergoes only one
(maybe two in the worst case) reflections. And even then the replacement of
aluminum (refl=0.7) by copper or brass (refl=0.85) improves the laser output
well. And silver or gold plated reflector (refl=0.95) may give 1.5 times
of improvement in comparison to aluminum one. This fact is proven both by
experiment and by calculations.
To change the reflectivity of the coating in the program You may in this
field of input:

As like as before it is outlined by red dotted line and pointed by red arrow.
A string below is the field of input for endRefl parameter - the reflectivity
of the endcaps of the reflector. Nobody forces You to make the endcaps of the
same material as the main surface of the reflector. Moreover, by setting this
parameter to zero, one can take a look, how the efficiency would degrade if
using no endpieces at all. To comprehend if one needs to use them or not.
Further on, one can note, that the efficiency of light transport from the
lamp to the rod depends sluggish on the oblateness of the ellipse, and on
moderate bias of its shape from mathematically correct one. The dependence
on the ratio of the ellipse mean diameter to the diameters of lamp and rod
and the dependence on small displacement of lamp and rod from the focal lines
is sluggish too. In its turn, it means, that one could use seriously oblate
ellipses without sufficient losses. It makes laser to be more compact,
lessens the losses to the ends, and, of most importance, it allows to
use bielliptic shape effectively. "Classic" says, that by using double
elliptic reflector and two lamps one can not achieve more energy deposition
in the laser rod, than it was with one lamp and one ellipse. One can only
achieve more uniform pumping. However this statement is true only for round
ellipses or when the rod is much thinner than the lamp. In other cases
application of bielliptic reflectors with two lamps gives sufficient gain
in the amount of energy that can be put into the laser rod (and thus the
output energy of the laser too). For example I was able to find (and use)
a bielliptic configuration, that gives energy deposition 1.6 times greater
than single ellipse of the same oblateness and by 40% more than single
round ellipse.
However here the things depends strongly on the initial conditions.
Particularly on the said ratio of the rod diameter to the lamp diameter. So
for Your particular task, You are better to find the optimal shape by
Yourselves. For doing this the calculator has a checkbox "cutoff":

Outlined by red dotted line and pointed by red arrow. If the checkbox is
checked, the code will "cut" the ellipse by a plane, that goes through the axis
of the laser rod. Thus You get the efficiency of a half of the bielliptic
reflector. Due to the symmetry, the efficiency of the other half will be the
same. The energy put to the rod will be the source energy multiplied by the
efficiency. (Keep in mind that the efficiency of the lamp itself is not 100%,
and most of its spectrum goes in vain missing the absorption lines in the
laser rod.) Since we have two lamps in bielliptic case, don't forget to
double the source energy. I.e. if You got, that, say, the half of bielliptic
reflector has its efficiency by 30% lower than the original full ellipse,
it means that the total energy put to the ellipse is HIGHER than in
full ellipse (because 2 * 0.7 = 1.4 > 1).
Having finished the design and calculations one may proceed to the
manufacturing. As You now know, small incorrectness of shape only slightly
affects the efficiency, so a good reflector can be obtained even by oblating
a round tube until its plastic deformation. It's a pity, but it is hard to
polish such a tube from inside, and it is even harder to control the quality
of polishing. In order to polish the tube one could cut it into halves, but
the remaining mechanical strains will relax in such a type, that the resulting
deviation from the correct shape, cannot be called even as "moderate". The
resulting cross section would more resemble lentil rather than ellipse or
even oval.
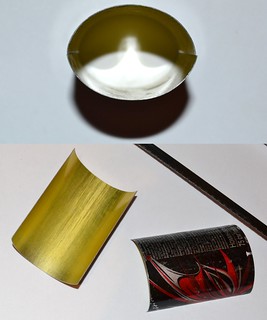
In order to preserve the shape, the oblate tubing should be enforced in some
way before the cut. For example, by putting it into some curb and by casting
it with tin-lead solder, as it was recommended by mister Rapp at his previous
site http://www.pulslaser.de/ in the article on dye laser. One can also cast
with some epoxy resin instead of the solder. The sequence of operations is shown
on the next picture.

Test reflectors based on deformed aluminum tubes cast with epoxy resin in
rectangular curbs were used successfully in my dye lasers with lamp pumping.
And there was only a minor difference between the efficiency of reflectors
based on plastically deformed tubes and the efficiency of reflectors based on
elastically deformed ones. (In theory the shape for the elastic deformation
should be more close to the correct ellipse.)
The separate word must be said on the endpieces. If Your laser has small
elongation (as it usually happens), usage of mirror-glossy endcaps at the
ends of the elliptic cylinder does significantly increase the efficiency
of the light transport from lamp to the rod.
In order to fullfill this the endcaps must be:
- namely mirror glossy (diffuse scattering must be low);
- flat;
- aligned so that the plane of endcap mirror be orthogonal to axis of
elliptic cylinder (and to axes of lamp and rod too). The precision of
the alignment here may be much lower than for the laser resonator, but
still the slant angle of only ten degrees will ruin all the gain, that
could be obtained from the endcaps.
The endcap mirrors of the elliptic reflector may be made not only of
polished metal. Mirror coated glass also suits well. Excellent results may
be obtained by using common ("household") aluminized glass mirrors, having
been cut to size and shape by diamond tools, and having indents for placing
lamp and rod.

Good results can be obtained with reflectors, based on 3D-printed shapes.
Generally the process is the next:
- Develop (or download) a 3D model of reflector
- Export g-code from Your slicer program
- Print
- Glue aluminum or copper foil onto the working surface of the reflector
(best result is of course with silver or silver coated foil)
- Polish the foil untill it becomes mirror glossy
- Print endpieces and make flat mirrors for them. One can use polished
metal or metallized glass. Optionally You can glue the mirrors to the
endpieces.
- Assemble all parts to the complete unit.
Step 4 needs some comments. It appears that it is not so simple to select
a glue, that would make strong bonds between metal foils and parts made of
PLA, ABS or PETG plastics. From my experience the best results here could
be obtained by using elastic glues. Like rubber glue and so on. However
with these glues the bond is not strong enough, so be careful when polishing.
Don't strip the glued foil from the surface of the 3D-printed parts.
Here are some usefull models to download:
Reflector cavity for rod, having diameter 5 mm and length ~30-50 mm, pumped
by a small photography lamp (being sold as lamp for SB-600)
DOWNLOAD

-
Bielliptic reflector cavity for rod, having diameter 5 mm and length
~30-50 mm, pumped by two small photography lamps (SB-600)
DOWNLOAD

-
Reflector for ruby rod, having diameter 8.5 mm and length 80 mm, for
(russian) xenon lamp IFP-800 aka INP3-7/80. Keep in mind that on the
contrary to four-leveled neodymium lasers, ruby has three levels an hates
non lit areas of the rod.
DOWNLOAD

-
Reflector for YAG:Nd rod, having diameter 7 mm and length 110 mm, for
(russian) krypton lamp
DNP-6/90.
DOWNLOAD

DIAGNOSTICS
Until You have tested elliptic reflector in laser You will always be bothered
by doubts whether the reflector works correctly, or whether the positions for
lamp and rod were chosen right. If Your reflector is able to be parted in the
plane, that contains focal axes, there is a simple method to get rid of these
doubts - to make a preliminary check, whether all things work properly or not.
Take a half of the reflector and put the laser rod into indents, intended
for its placement. (One could use any rod of proper size here, even if it
was a pencil.) Then look into the reflector through the place, where the lamp
should be. The indents for the lamp in the endpieces will give Your a hint
where to look. If reflector works properly, You should see reflection of the
rod at the place, where the lamp should be. This phenomenon takes place almost
independently on the angle of view. Only the size of the image will change a
bit with changing this angle.

The same can be observed, if the lamp (or its model) was installed to its place,
when looking to the reflector through the place, where the rod should be.
- Bela A. Lengyel. Lasers, Second Edition. (C) 1971, by John Wiley & Sons,
Inc. ISBN 0 471 52620 7.
- W. Brunner, K.Junge. Wissenspeicher Lasertechnik. VEB Fachbuchverlag
Leipzig, 1987.
ISBN 3-343-00204-6
<< HOME PAGE |